PCB打样和PCB生产之间的区别主要体现在以下4个方面:
一、目的与阶段
PCB打样
目的:主要是在产品设计阶段,用于测试和验证电路设计的正确性和功能性。它通常发生在批量生产之前,用于原型制作或小规模测试。
阶段:属于产品研发的早期阶段,是硬件开发从构想到量产的第一步。
PCB生产
目的:在产品设计定型并经过市场测试后,为了满足大规模市场需求而进行的生产。
阶段:属于产品研发的后期阶段,是产品量产的过程。
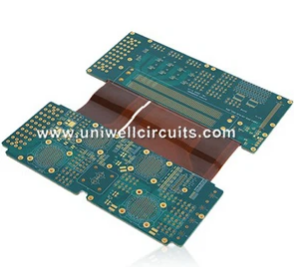
二、生产特点
PCB打样
灵活性:更注重快速响应和灵活性,以适应设计上的快速迭代和修改。可能采用更灵活的生产工艺,以适应设计上的快速变化和修改,可能更多地依赖于手工操作和小规模的自动化。
订单规模:通常订单面积较小,一般不超过5平方米,生产数量也较少,可能只有几个到几十个单位。
成本控制:由于数量少,通常单位成本较高,价格相对较贵,因为生产过程中的固定成本(如设置费用、工程费用等)需要分摊到较少的产品上。
交货时间:通常要求快速交货,以支持产品开发的快速迭代,交货时间可能从几天到几周不等。
质量控制:可能不会进行严格的质量控制和测试,因为主要目的是验证设计,而不是生产最终产品。其质量控制可能更依赖于设计验证和测试,而不是生产过程的质量保证。
PCB生产
生产效率:更注重生产效率、成本控制和质量保证,通常由具备大规模生产能力的工厂承担。
订单规模:订单面积较大,通常在50平方米以上,生产数量可能涉及成千上万的单位。
成本控制:由于规模效应,单位成本较低,价格更具竞争力,因为固定成本可以分摊到更多的产品上,而且可以通过自动化和优化生产流程来降低变动成本。
交货时间:虽然也追求交货效率,但由于生产规模大,生产周期和交货时间相对较长,可能需要几周到几个月的时间来完成订单。
质量控制:需要经过严格的质量控制流程,包括原材料检验、在线测试、最终检验等,以确保产品的一致性和可靠性。批量生产中的任何质量问题都可能导致大规模的召回或返工,因此对质量控制的要求非常高。其生产工艺高度自动化和标准化,以提高生产效率和降低成本。
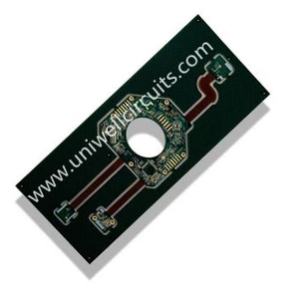
三、应用场景
PCB打样
广泛应用于高校教学与实验室研究,学生和科研人员可以通过实际操作了解从设计到制造的全过程,提升实践能力。
适用于新产品研发,因为新产品研发往往涉及反复的设计迭代,PCB打样提供了低成本的试验机会,帮助开发团队在实际应用场景中验证设计效果。
适用于某些特殊项目,如医疗设备、工业控制电路等,这些项目需要定制化的PCB设计,打样可以快速响应客户需求并验证方案的可行性。
PCB生产
适用于市场需求量大、产品已经定型并经过充分测试的情况。
适用于需要大规模生产以降低成本和提高生产效率的电子产品。
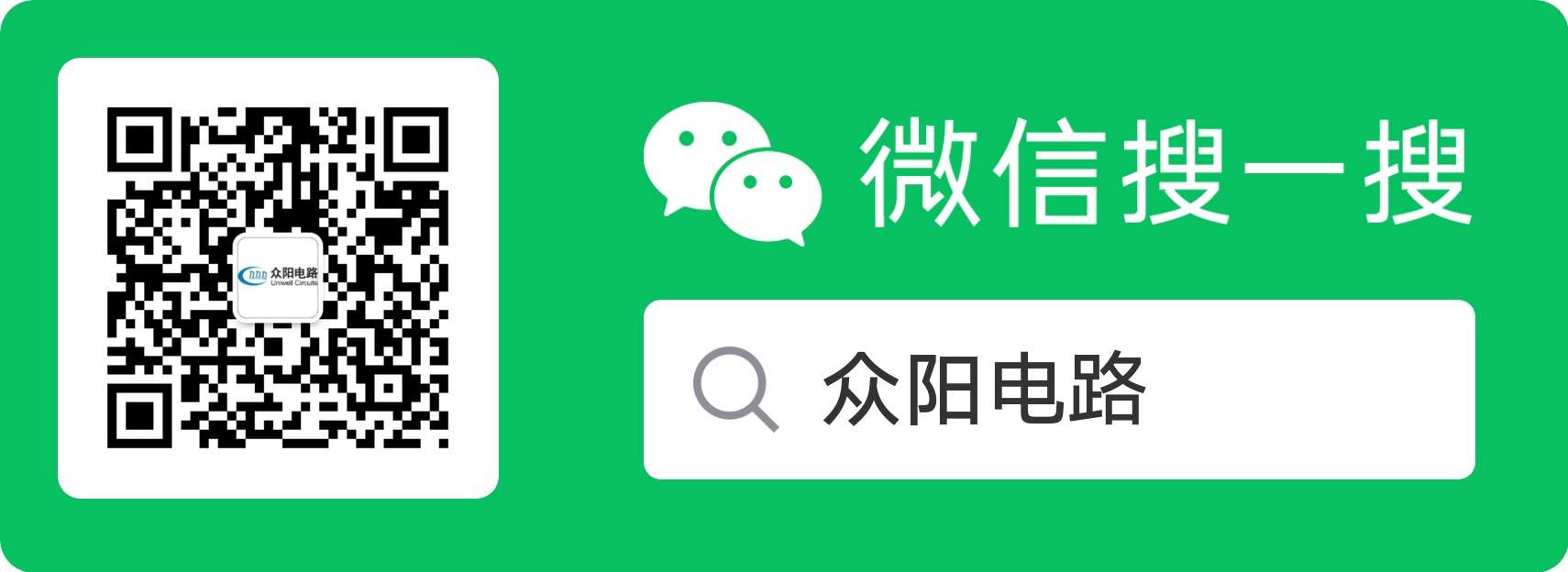